Engie’s new energy-positive drying and storage process is already yielding good results in the Netherlands and Germany. De Aardappelhoeve in Tielt, West Flanders, is the first for our country. This energy-positive system will be implemented in a new warehouse that will house 4,000 tons of potatoes and 4,000 tons of onions and shallots.
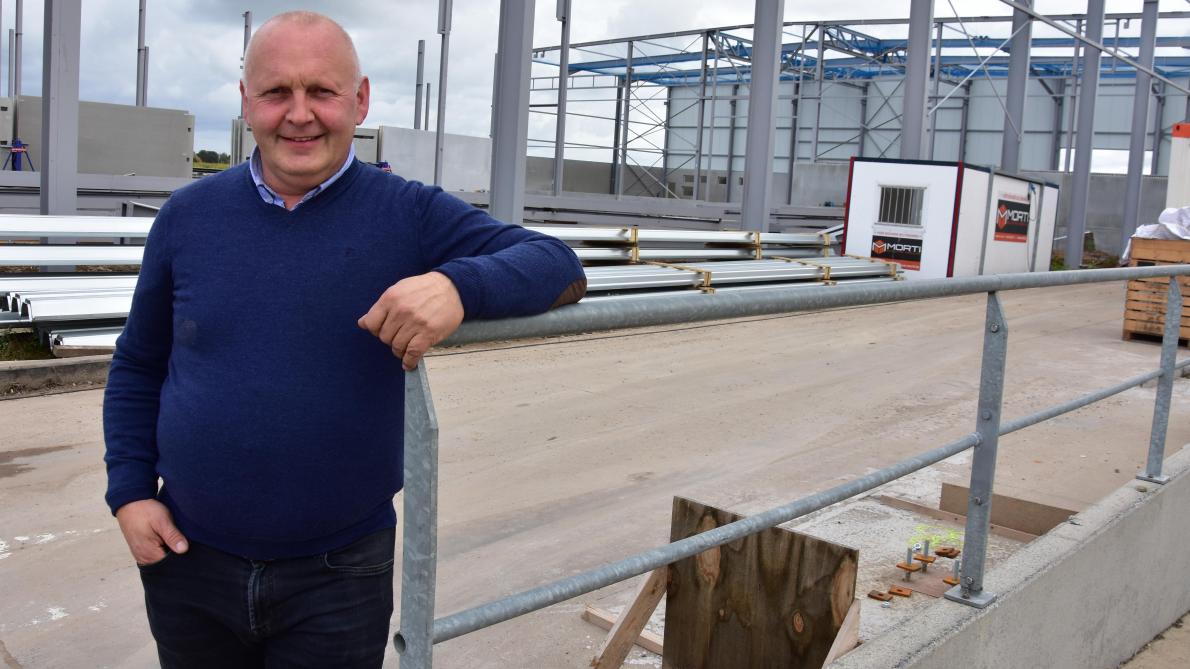
By the beginning of next year at the latest, the new drying and storage shed of Bart Nemegheer’s De Aardappelhoeve will be operational. It is a large industrial warehouse, which should equip the potato and onion processing company even more for the future. The new construction is not only there to reduce the rent of necessary warehouses elsewhere, but mainly because it offers new opportunities in the field of sustainability, among other things.
Cargos full of food
The story of the food on our plates is well known: large cargo flights are used to bring in beans from Kenya, pineapples from Ghana and strawberries from Australia. In addition to the impact on the environment, due to the long transport distances, these products also require a longer storage time, intensive cooling, additives, chemical crop protection agents. That is often unhealthy and environmentally unfriendly. Partly at the request of retailers, De Aardappelhoeve wants to be able to offer Belgian buyers agricultural products from here for longer.
“In the future, this will allow us to further reduce the import of, for example, early potatoes from Italy and Spain, and certainly also from Israel,” says Bart. “We would then be able to feed the consumer with our Belgian top products for longer.”
However, an adapted system is needed to keep our Belgian fries longer shelf life. “The outside air that is now often used for the drying and storage of potatoes offers us little perspective. And that includes the new regulations, but also climate change to a large extent. Changes in temperature, humidity and CO2 can affect the potatoes and cause them to dry out. The chance of rot nests, pressure spots and germs also increases.”
Keep longer
And if the domestic quality becomes insufficient or if there is insufficient supply, potatoes must be imported from southern countries. All the more reason for De Aardappelhoeve to team up with Engie for the furnishing of the new warehouse. “We will be the first in our sector to use this technology,” says Bart. “We started looking at examples in Germany and the Netherlands.”
An Engie concept will be placed in the new warehouse Refrigeration . It is a drying and storage process that will make farms no longer dependent on the outside air. “This will enable us to supply high-quality products all year round.” The system is therefore called a climate-positive drying and storage process.
Condensation drying
Condensation drying technology forms the basis of this innovative drying and storage process. “This allows agricultural products to be dried and stored in combination, without being dependent on the unpredictable outside air and energy-guzzling gas stoves.”
The condenser dryer is in fact a hybrid cooling and heating installation in one machine. The air is brought below the condensation point in the drying and storage room, so that a lot of moisture can be removed and the potatoes are dried. The heat released during the cooling process is then reused, for example, for heating other buildings and process water. In this way a positive energy compensation is achieved. The system is also equipped with an energy-efficient heat pump, which means that it can be used to heat batches for combating diseases.
“The heat pump uses the heat released during the cooling process (drying process) to heat up the crops or to maintain the temperature. Because the system is not dependent on the outside air, no heat is lost during heating either,” explains Bart. The drying of the potatoes continues during heating. Only a fraction of electricity is required for this. Incidentally, it is also sustainably generated by solar panels.heat is lost”, Bart explains. The drying of the potatoes continues during heating. Only a fraction of electricity is required for this. It is also sustainably generated by solar panels.
Without gas consumption
“The mechanical cooling always ensures a stable temperature and humidity during the storage of the potatoes, which helps to maintain the quality of the product. Precisely by excluding the outside air, we can precisely control the ideal drying and storage conditions. Without gas consumption and less CO2 emissions”, Bart explains.
“And because we generate a lot of energy with solar panels and reuse residual heat, we supply more energy than we need on an annual basis.” The solar panels that will be installed have a capacity of 621 kWp. These are 1,656 panels of 375 Wp each. The expected annual yield of solar energy is 603,000 kWh. Due to sustainable generation, the saving in CO2 emissions amounts to 335,000 kg per year. The condensation drying system has an energy consumption of 513,000 kWh per year.

Use solar panels
“Because we generate a lot of energy with solar panels and reuse the residual heat, we supply more energy on an annual basis than we need for the condensation drying system. With this we realize a concept with a positive energy compensation or energy balance”, Bart continues. “In addition, a CO2 saving is also achieved.”
Compared to a conventional system, with synthetic refrigerants or CO2/DX, in combination with the use of gas heaters to dry the product, the CO2 savings for cooling and cooling are storage process 158,000 kWh per year, which is equivalent to a CO2 saving of 88,000 kg CO2. For the drying process, this involves a saving of 117,000 kg of CO2, or a combined saving of 205,000 kg of CO2 per year.
Monitoring and steering
High-tech measuring, regulation and control technology is playing an ever-increasing role in the agricultural business. “By developing ICT applications such as (product) sensoring and remote control , you can monitor and control better and better on the basis of real-time data.”
For example, the sensors measure the environmental conditions, the product temperature and the degree of dehumidification by means of a condensate discharge registration. Together with the Engie computer, De Aardappelhoeve will soon be able to monitor the current situation in storage 24 hours a day. The conditions in the storage can be adjusted via an app to create the optimal conditions.