From generational farming to cutting-edge sustainability practices, the Masser Family of Companies exemplifies modern potato processing.
When it comes to championing sustainability, it’s hard to beat farmers, ranchers and vertically integrated food & beverage companies — especially generational ones. Enter the Masser family, an eighth-generation potato farming family in Sacramento, Pa., which has grown into the Masser Family of Companies, a vertically integrated potato production and processing business — and winner of our 2024 Green Plant of the Year poll.
The Masser family first emigrated to what is now the Reading, Pa., area in 1754, and the next generation began growing potatoes, says David Masser, current CEO of the Masser Family of Companies. In 1970, Masser’s grandfather started Sterman Masser Inc., and 54 years later, the Masser Family of Companies encompasses four businesses: Sterman Masser, Keystone Potato Products, Masser Logistics Services and Lykens Valley Grain, which provides the cover crops used in rotation on the potato farms.
“The majority of our sales are to retailers across the country,” Masser explains. “Every product that’s in that fresh potato category is something that we would provide.”
As Masser grew over the years, producing potato products while minimizing waste became more complicated than simply planting, picking and packing.
“As our sales and distribution company continued to grow, we found ourselves with a tremendous amount of off-grade potatoes that would not make the specifications for fresh table consumption,” Masser says. “We didn’t have a good use for that off-grade, so we were trying to figure out another way to generate value from that waste.”
That’s where the idea for Keystone Potato Products was born about 20 years ago. Keystone opened in 2005, featuring a dehydration line to turn off-grade potatoes into potato flakes and flour, which has helped Masser garner added value from its potato waste stream.
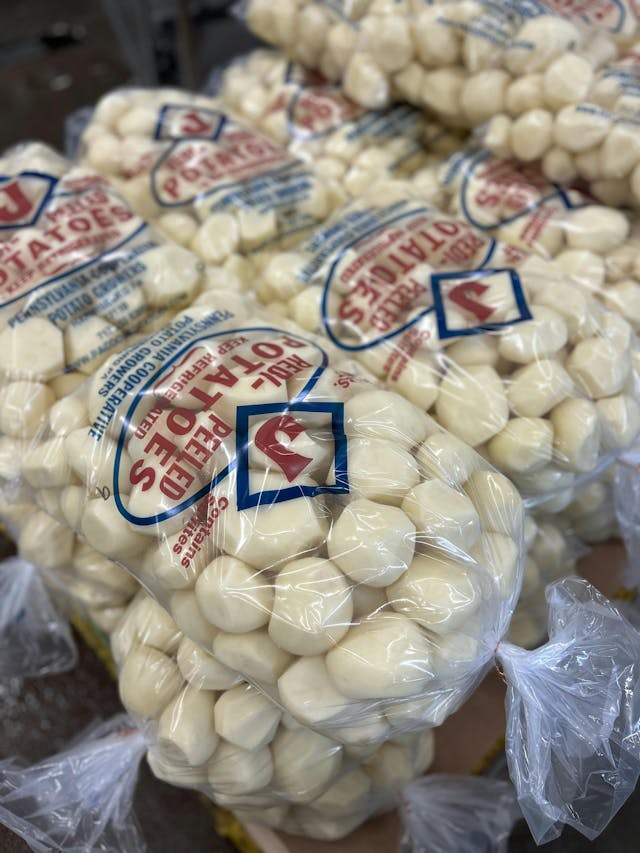
The 120,000-sq.-ft. facility also produces bulk dices, slices, wedges and fries on a high-capacity french fry line; 30-lb. bags of whole peeled potatoes for foodservice; retail fresh-cut potato products; 3- and 4-potato russet trays for retail sale; and multiple sizes of retail bagged fresh potatoes on two high-speed automated packing lines.
With the number of potatoes needed for these products, off-grade spuds were bound to increase.
“The [potato] waste that was created prior to Keystone had to go to cattle feed because you didn’t have enough outlet for the off-grade,” Masser explains. “That’s really what has helped us in the past 20 years with Keystone: Having value for that off-grade product has really been exceptional.”
Upping the ante on full utilization at Keystone: Central Pennsylvania has a significant chipping potato production stream, given the number of snack food processors in the region. But chipping potatoes are different. Masser says off-grade or off-size chipping potatoes were being used to supplement bagged retail potato products, but that led to poor consumer experiences.
“If you’ve ever cooked a chip potato for something other than chips, it’s a horrendous cooking experience,” he says. “They don’t taste good; they cook away in the water — it just makes for a very bad experience in the kitchen.”
Masser says the problem was so widespread that the company began to see demand for fresh table potatoes slumping because consumers couldn’t be sure that they were getting good, table-stock potatoes in the retail bags. But chipping potatoes make great processed potato flakes, and those off-grade chipping potatoes found a new home through Keystone’s process.
“There were no dehydration processing plants east of the Mississippi at that time, so Keystone filled a void,” Masser adds. Additionally, it has offered farmers a type of insurance policy in the event of rough weather.
“We give the growers confidence that if Mother Nature kicks in and doesn’t give us the best growing conditions, we have options for that off-grade potato,” Masser says. “There’s always going to be a home for every potato — we’re not out there dumping it on the field or feeding it to cattle, we’re making a value-added product from it.”
Converting pollutants to facility power
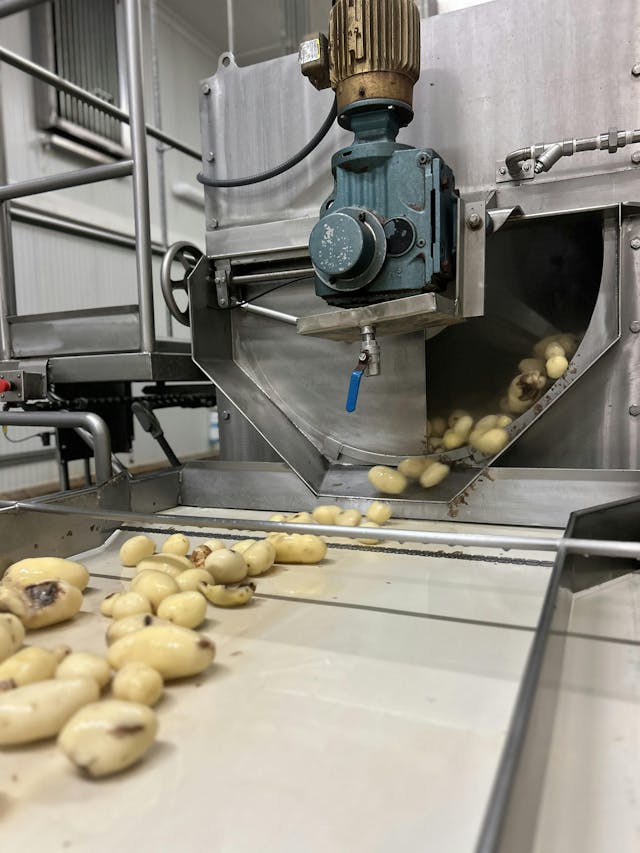
With water content of about 80%, potatoes require a lot of energy to be properly dehydrated, and Masser sought a low-cost energy source for Keystone that would allow it to be competitive in the market. Various alternative and renewable energy options arose, but ultimately, a nearby landfill was looking to expand and have the methane it produces used in a sustainable way.
“We were able to partner with the landfill to capture the methane gas, pipe it to our production facility and use that as the fuel source to create the steam to use in our process,” Masser says. Keystone Potato Products was built next to the landfill and still uses that methane as its energy source.
Additionally, the Keystone team wanted to be as sustainable as possible with regard to the water it needed for processing. For the first two years of the plant’s life, Keystone tapped into the standard water supply, but that source ended up not meeting the plant’s capacity demands, and the company needed a new water source.
“Underneath the ground the processing plant sits on was an abandoned coal mine pool — basically an underground lake,” explains Masser. “We had all these abandoned mine pools from the anthracite coal industry, and the water in them is contaminated, but there’s plenty of it. So how do we tap into that? Is there a mutually beneficial way to clean that water up and help the environment?”
The company didn’t need to invent a process, but the process used to clean the water to potable levels has changed, says Michael Peichert, executive vice president of strategic development, for Masser Family of Companies, who oversees Keystone Potato Products.
“We were able to remove iron and manganese with our original sand filters, but it was horribly costly,” Peichert says. “In 2014, we expanded our water treatment plant to be able to better remove iron and manganese.”
The water goes through a series of cleaning steps, and the iron and manganese (the primary metals in the water Keystone uses) precipitate out with the addition of a chemical additive. Keystone uses that drinkable water in its plant, then sends it to its on-site wastewater treatment plant, and the cleaned water is discharged into the local watershed.
“Ultimately, we clean impaired mining water that would otherwise degrade the environment, use it to process food, then treat it again before discharging it,” Peichert says.