Agribusinessglobal: today, 50% of shipping containers are considered late, says Keith Holdsworth, a senior supply chain consultant with Perfection Limited, based in West Oxfordshire, England.
“Assumptions are that for various reasons up to 25% of deliveries by ships will be delayed or orders cancelled,” adds Stephen Pearce, director, AWP Associates, a professional sourcing organization with deep knowledge of the AgChem manufacturing and material supply sector. “Orders for shipping in general have hit a 17-year low.”
The reason: Ships are stuck at ports for days in floating traffic jams. Pandemic restrictions have limited dockworker and truck driver availability. If a container can’t be unloaded in one place, it can’t be loaded in another.
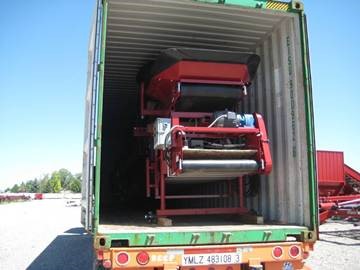
“I’ve never seen anything like this,” said Lars Mikael Jensen, head of Global Ocean Network at A.P. Moller-Maersk, the world’s largest shipping company, in The New York Times. “All the links in the supply chain are stretched. The ships, the trucks, the warehouses.”
To try and make up time, vessels are also staying docked for less time than originally planned. “So maybe they were scheduled to be there for 10 days, but because they are trying to make up time in their schedules, they leave in two days with a container that isn’t full,” Holdsworth says.
This means last-minute purchasing is no longer an option. “The opportunity to spot-purchase a product and catch a vessel before it sails is not possible today,” Pearce explains.
“Pre-COVID, you could get a product moving in two weeks, Holdsworth adds. “Now it takes at least six to eight weeks.”
Holdsworth says people are responding by using “a bunker mentality” where they are trying to cover their own situations as best they can.
“People are even trying to pre-book space in a container and pay for it before they even know what product they are going to move,” he says. “This blocks up capacity longer.”
The companies that suffer the worst are those that don’t plan well. “As they say, ‘Failing to plan is planning to fail,” Pearce says.
Successful companies are embracing long lead times. “They have to regularly check where their orders are in the make-move-ship cycle,” he urges. “Plan several months ahead. Secure as much of your forecast volumes ahead of time. Then confirm and reconfirm that containers are secured and sailing times are known. Check and check again.”
Firming prices to avoid overpayment is also a wise move, Pearce advises.
Shipping Containers Remain Hard to Secure
Containers arrived on the scene in 1956, revolutionizing global trade. They came in standard sizes, making it easy to load and move them by cranes, trucks, trains, and ships.

As shipping delays amplified during the pandemic, containers became harder and harder to come by, yet imports increased. According to S&P Global Market Intelligence’s Panjiva, total U.S. imports of containerized freight surged 20% in February compared to last year and 15% more than in February 2019, extending a record sixth straight month of double-digit growth and signaling that congestion issues will continue through the summer.
China produces 96% of shipping containers in the world, Pearce says. As a result of the apparent lack of containers, China has been manufacturing 300,000 containers every month since November-December 2020, Pearce explains. “But this increase has still been unable to keep pace with increased demand,” he adds.
While this means container space availability isn’t as bad as it was, the problem now is the lack of vessels to put the containers on. “We have more boxes to put stuff in, but fewer ships to carry the boxes,” he says. Unfortunately, bigger boats aren’t the answer. “As boats get bigger, they become less stable in stormy weather, increasing the risk of losing shipments,” Holdsworth explains.
Freight Rates Remain High
Experts expect freight rates to stay high for the next two months. They have come down a little bit from their really high peaks, but they are still two to three times what they were a year ago, Holdsworth says.
“A lot of carriers tried to sail through Chinese New Year to create a small surplus of available capacity,” Holdsworth points out, hoping there would be a drop in prices as a result. “But as we went through that period, rates stayed flat to where they were, which is still at a pretty high premium.”

The bright spot is that “Chinese suppliers we’ve talked to are saying it’s peaked in terms of pricing,” Pearce says, “but the reset will be gradual and take longer than people originally anticipated.”