BESIDES COOLING CROPS, HIGHER SPEED PIVOTS CAN BE IDEAL FOR CHEMIGATION AS WELL AS WATERING JUST-PLANTED SEEDS.
There are times you wish your pivot could make a trip around the field a little bit faster … maybe even twice as fast. The convenience of that feature becomes apparent when it’s necessary to move the pivot out of the way when planting or harvesting.
Yet, higher speeds that allow watering at twice the normal speed bring myriad agronomic advantages. For example, a light application can be employed to cool crops, gain precision in chemigation and foliar applications, or light watering in of small-seed crops that were just planted.
There are now two speed options available. The first appeared two years ago when Valley introduced its X-Tec Drive with a top speed of 37.5 feet per minute. That allows a seven-tower pivot to make a full revolution in about four hours.
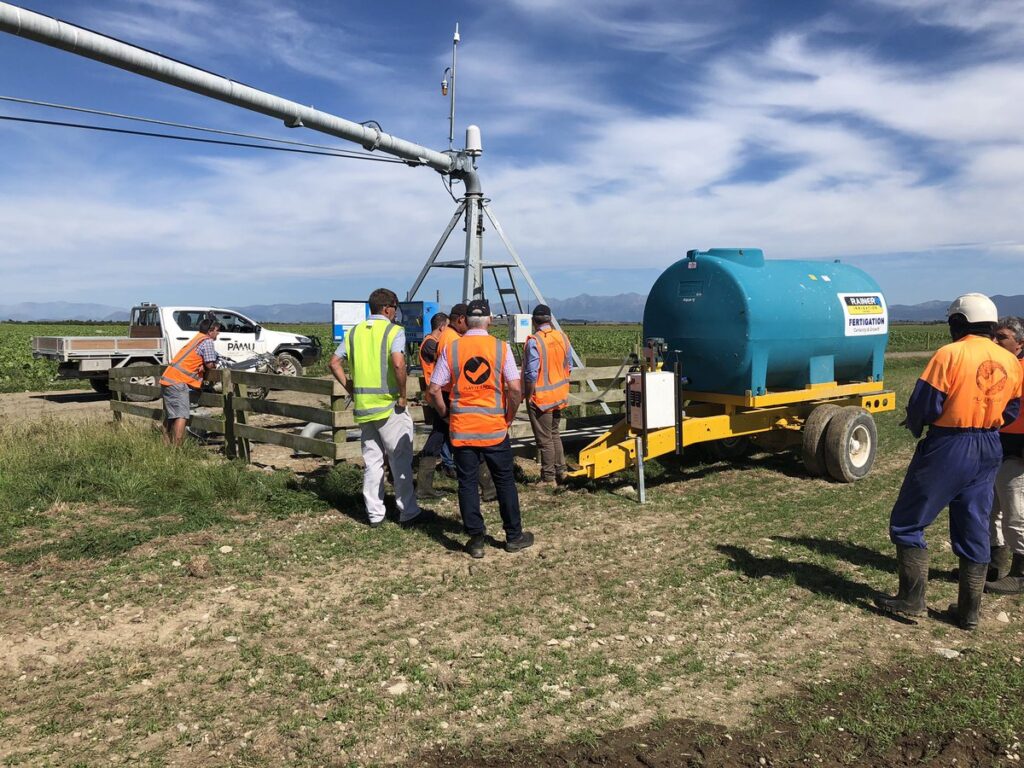
According to Chris Righter with Valley, the X-Tec Drive combines an advanced DC motor with its patented FastPass technology to provide constant torque throughout a wide speed range across any terrain.
Then, last year Lindsay joined the ranks of high-speed pivot makers with its Zimmatic 9500HS. According to Wade Sikkink of Lindsay, the 9500HS uses a high-speed center drive motor that will operate at twice the normal speed to cover a circle in half the time, but it can also be set at half speed for normal rotation.
Both the Valley and Zimmatic systems can be retrofitted to an existing pivot by changing out the appropriate components, including the center drive motors.
SPEEDS OF TYPICAL PIVOTS
Meanwhile, Ken Goodall at Reinke Manufacturing points out that, “With today’s high-speed motors on center pivots, and the use of tall tires, a quarter-mile-long center pivot can easily make a full rotation in under seven hours. Higher speeds can be accomplished if needed, but they are rarely required.”
On the other hand, Dave Thom of T-L Irrigation, explains his company can configure a pivot to match nearly every customer’s specifications, including high-speed travel.
“The average quarter-mile pivot is designed to apply one-third inch of water per revolution,” he says. “However, since all of our pivots are hydraulically driven, and nearly every one of our pivots is custom designed for the application, it’s just a matter of configuring the hydraulic pump and oil lines to attain the speeds the customer needs,” Thom explains. “Our hydraulic motors don’t have a set RPM like an electric motor, so we’re still not hitting the maximum speed of the motors, even if we design a pivot that can make a full revolution in six hours.
“The thing we always push is the continuous movement of hydraulic drive at any speed,” Thom says, noting that nonstop movement is the main feature DC motors on electric pivots now offer. “If you’re putting on a fungicide or pesticide at high speed, you don’t want inconsistency; and the faster the pivot moves, the more pronounced spoking and drivetrain wear become from starting and stopping.”
The need most often mentioned for high-speed pivots is for chemical application, Sikkink relates. “It allows you to apply a chemical much faster, plus, it allows you to apply chemicals at a higher concentration, which is necessary with some products.”
CHEMICAL CONSIDERATIONS
According to Troy Peters, professor of biological systems engineering at Washington State University, a number of herbicides and pesticides (especially those applied to control pathogens like rots, molds, and wilts) need to be applied in a concentration that allow the chemical to stay on the leaves. If a pivot moves faster than normal, it can apply less water along with a more concentrated chemical application so the chemical doesn’t run off the leaves.
In contrast to an irrigation system, which has the objective of getting water into the soil, a faster pivot can apply chemicals in a manner closer to that of a sprayer, whose objective is to get the leaves wet.
Valley’s Righter agrees that high-speed irrigation also allows corn producers to quickly apply a late-season fungicide. Instead of paying for an aerial application, producers can apply the chemical at twice the normal pivot speed with a minimal amount of water.
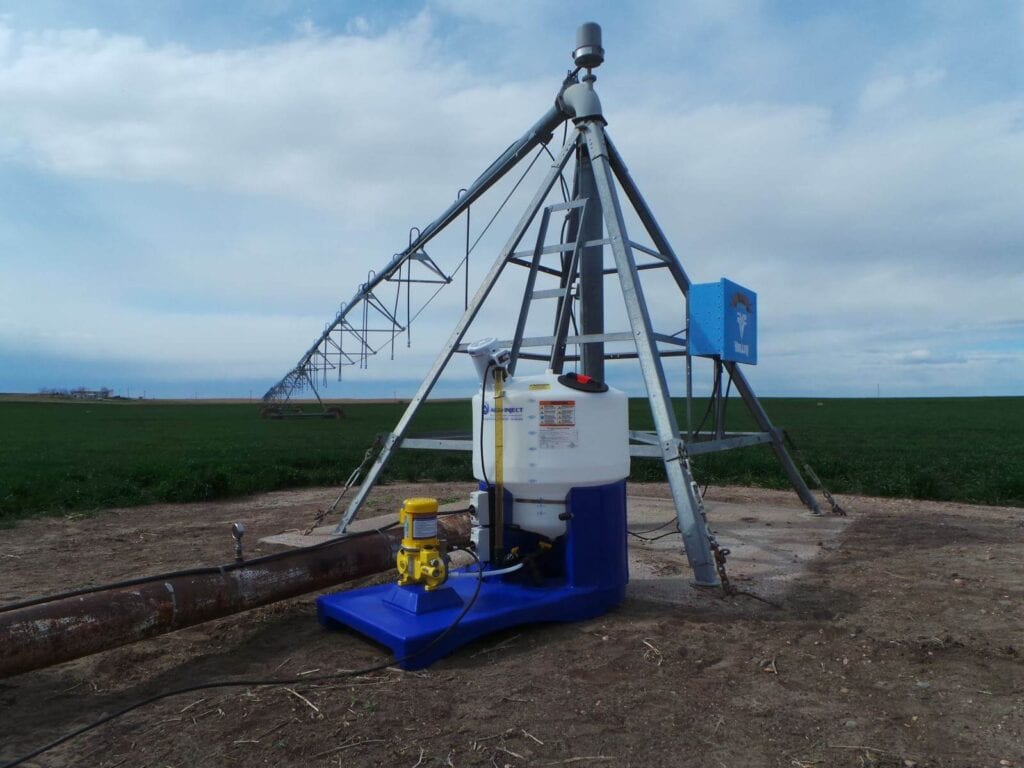
Equally important, high-speed irrigation allows producers like the Grimm brothers, who own Precision Farms near Hiawatha, Kansas, to cool corn on extremely hot days.
COOLING DOWN CROPS
Noting that the temperature in the canopy is often 10°F. higher than the outside temperature, Precision Farms manager Galen Grimm adds, “I can have the pivot make two cooling passes in an afternoon when it’s 105°F. At full speed, it only takes about 1½ hours each way. We can cool our crop with a quick rotation and send it around again, all in one afternoon,” Grimm adds, noting that they also use the pivot to chemigate at low water amounts.
Sikkink points out that the ability to make faster chemical applications has been particularly appealing to potato farmers and vegetable growers who need to cool heat-susceptible crops on hot days. It also allows the grower to apply frequent, light applications to maintain a wet soil surface after planting, keep small seed from blowing away, and improve germination.
More recently, though, alfalfa growers have seen a benefit from high-speed irrigation. As Sikkink explains, alfalfa growers typically stop irrigation five to seven days before harvest, which puts a lot of stress on the plant.
“With high-speed irrigation, they can continue to make light, frequent applications to keep the canopy cool and wet, while the plants dry from the ground up,” he says. “This lets the grower wait until about three days before cutting to stop watering. Then, as soon as they get the hay off the field, they can start watering again. Since the plants have now gone fewer days without water, they bounce back faster, and research has shown that yields are actually higher.
WELL FLOW RATES DO DROP DURING THE SEASON
Research by the University of Arkansas discovered flow rates from wells often decrease during the season. That investigation found that six out of 28 wells in that state experienced discharge decreases of more than 30% during the summer. The average decline was 19% for all wells.
Darrel Martin and Derek Herren at the University of Nebraska warn that well discharge is also experienced in the Great Plains, “but we do not have specific data such as from Arkansas,” they say. “The point is that many pivots face changing flow rates during the season. Since many pivots utilize pressure regulators, the pivot inflow cannot exceed the installed or design flow. Thus, pivots must be operating well below conditions used in the initial design.”