In recent years, the agricultural industry has become rapidly automated. Whether it concerns sorting, processing, weighing or packaging – more and more fully automated solutions are being used. The purpose of this automation is to save personnel and therefore labor costs. Precisely because of the current corona regulations – the distance rules and the wearing of mouth masks – this need has only increased, says Oliver Werner – sales manager Germany of the machine and installation group Upmann.
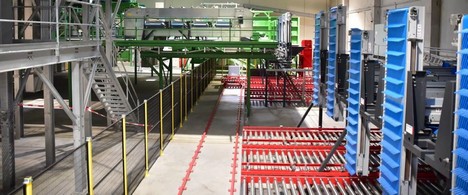
Regional agricultural products are especially appreciated in times of corona. Many of these foods – vegetables, fruit and potatoes, for example – are now increasingly sourced from regional farm shops. “Direct sales are clearly experiencing a revival. This is reflected in the need for appropriate machine equipment,” explains Oliver.
New packaging procedure
He cites as an example the packaging installation for paper bags type 4405, a recently presented optimization of the model 4404 launched in 2018. “With the help of this machine, potatoes, onions and co are quickly and easily into the desired packaging size – from 0.5 up to 5 kg – packed. ” This installation is suitable for large packers as well as smaller direct sellers with an area of around 10 hectares. “The machine is also profitable for the latter users within a few years, because the products are packed three to four times faster than with manual packaging.”
Noticeable automation trend
In general, automation is the keyword in today’s agricultural sector, Oliver believes. “Technology for high-bay warehouses is one of our hobby horses. But the optical sorting procedure of our partner Visar for carrots or potatoes, for example, is also well received.” The need for highly automated solutions is not limited to the conventional market. “The willingness to invest in organic and Demeter companies has – in parallel with the rapidly growing consumption – developed in recent years.”
Corona has once again significantly accelerated the demand for highly automated solutions as the need to save more staff due to tougher working conditions has now increased even more,” continues Oliver. The automation trend will also continue after the crisis, he predicts. “Any sector that can be automated – whether it concerns sorting, processing or packaging – will develop further in my opinion.
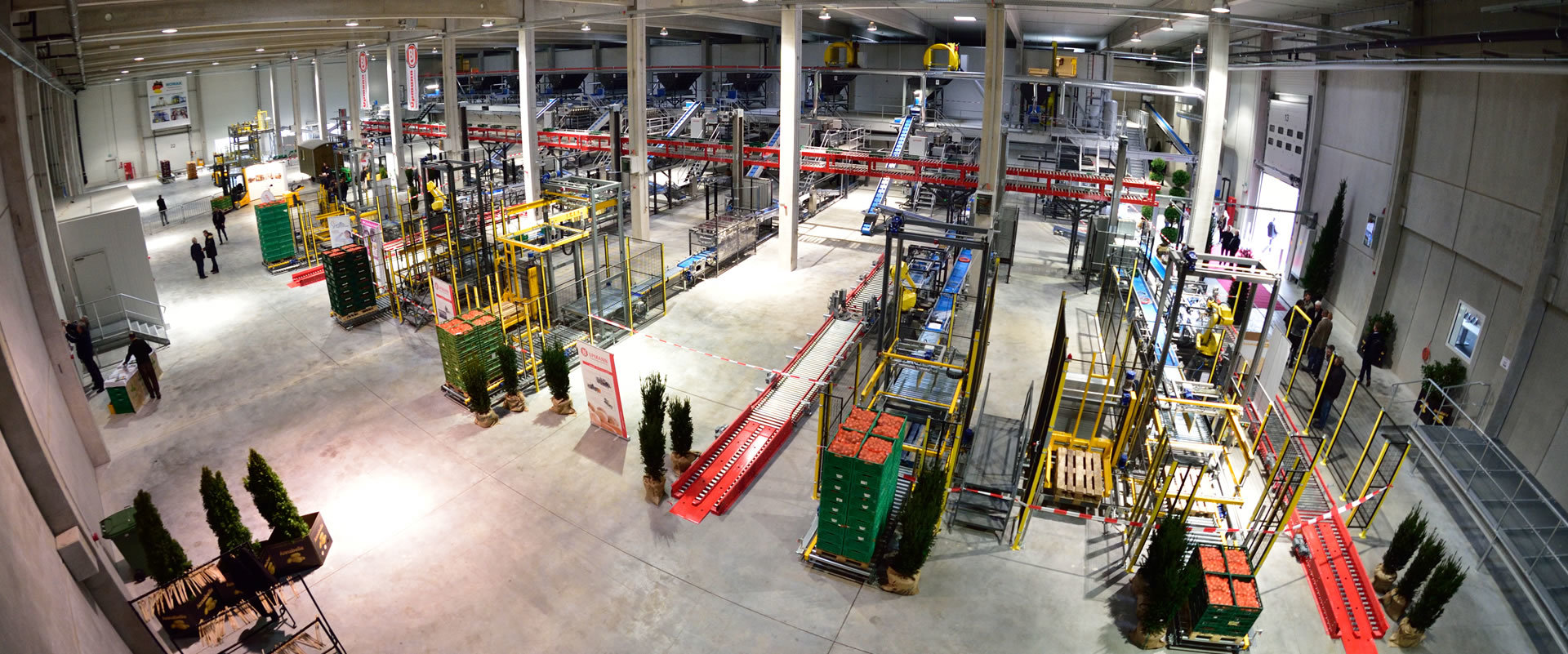
Differentiation in potatoes
Next year, Upmann will celebrate its 225th anniversary and its roots lie in the potato sector and vegetable storage. Precisely in the potato industry, onion industry and carrot industry, the accuracy during sorting has increased considerably. “On the one hand they want to work more accurately and on the other hand produce less waste. Instead of three or four categories – for example normal potatoes, oversized potatoes and new potatoes – modern potato sorting installations are now equipped with six outlets. selling product has become more extensive “, Oliver concludes.
For more information:
Upmann Verpackungsmaschinen GmbH
Oliver Werner
E-mail: oliver.werner @ upmann.de
Internet: http://www.upmann.de