For the 2022 season, GRIMME presents the completely newly developed store loaders of the SL 900 and SL 700 series, which combine the highest throughput rates with optimum crop protection and user-friendly operation. The store loaders can be used to store potatoes, onions, red beet, celery and other bulk goods, among other things.
SL 900 series – The new excellence class
The new SL 900 series represents the advanced development of the proven SL 80 series. Compared to the previous model, the belt width has been increased from 800 mm to 900 mm. The trough shape of the conveyor belt has also been optimised with regard to the conveying cross-section. This means that even higher throughputs can be achieved.
Alternatively, a reduced belt speed can be used for smaller throughput quantities, which has a positive effect on crop protection.
The SL 900 series includes two models, the SL 916 with conveying lengths from 9.7 m to 16.5 m and the SL 919 with conveying lengths from 11.2 m to 19.5 m.
As an option, the “Quantum feeding conveyor” is available for both models, which ensures a constantly low drop height, regardless of the swivel angle of the store loader. Moreover, the Quantum feeding conveyor enables larger swivel widths of up to 180° and an increased storage performance through optimised crop flow.
The Quantum feeding conveyor increases the conveying length of the SL 916 to 17.7 m, resp. to 20.7 m when the SL 919 is in use.
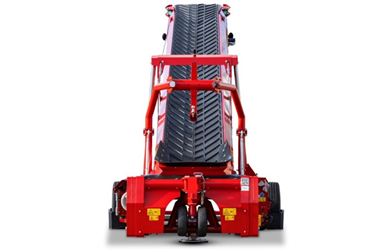
SL 700 series – With Quantum in-feed conveyor and intelligent potato store filling functions
The new SL 700 series of store loaders are equipped with a 66 cm wide and 16.5 m long conveyor belt. This machine can also be equipped with the optional available Quantum in-feed conveyor. This means that a maximum conveying length of 17.7 m can be realised.
Like the SL 900 series, the SL 700 series now also has the new store house filling functions and a new, intuitive operation.
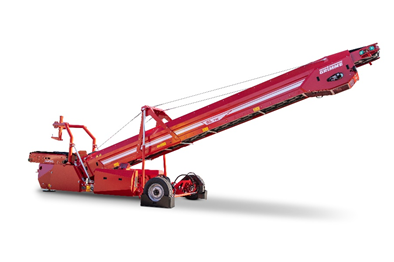
More convenience thanks to new store filling functions
With the new warehouse fillers, three new store filling functions are available:
StoreMatic-BASIC
With this store filling function, the change of the swivelling direction takes place as soon as the optical sensors on the chassis detect the freely positionable limiting tables. For an even height of the crop when bulk storing, the pause time in the corners can be adjusted manually.
StoreMatic-PLUS
The optionally available StoreMatic-PLUS filling function is able to detect store walls or obstacles with the help of ultrasonic sensors at the upper end of the conveyor. In addition, the automatic system detects inconsistent heights when loading the crop and levels them out by reducing the swivelling speed. Alternatively, the store loader can automatically retract the telescopic conveyor belt at the reversal points or lift it independently.
StoreMatic-PRO
This premium option includes the functionalities of both the StoreMatic-BASIC and the StoreMatic-PLUS as previously described. Alongside these options StoreMatic-PRO is also supplemented by further intelligent functions.
The setpoints of the swivel width can be set independently on the right and left. These values can even be adjusted in the storage process via the operator terminal CCI 800.
In addition, corner filling, an automatic level change as well as a continuous adjustment of the crop-discharge height and the individual setting of a maximum storage height are available.
With the StoreMatic-PRO, the user has three presets for the storage process ex works: Maximum performance, maximum crop protection or a middle way between high performance and high crop protection at the same time. With these presets, setting the required values of the store loader is much more intuitive.
More convenience thanks to new store filling functions
With the new warehouse fillers, three new store filling functions are available:
StoreMatic-BASIC
With this store filling function, the change of the swivelling direction takes place as soon as the optical sensors on the chassis detect the freely positionable limiting tables. For an even height of the crop when bulk storing, the pause time in the corners can be adjusted manually.
StoreMatic-PLUS
The optionally available StoreMatic-PLUS filling function is able to detect store walls or obstacles with the help of ultrasonic sensors at the upper end of the conveyor. In addition, the automatic system detects inconsistent heights when loading the crop and levels them out by reducing the swivelling speed. Alternatively, the store loader can automatically retract the telescopic conveyor belt at the reversal points or lift it independently.
StoreMatic-PRO
This premium option includes the functionalities of both the StoreMatic-BASIC and the StoreMatic-PLUS as previously described. Alongside these options StoreMatic-PRO is also supplemented by further intelligent functions.
The setpoints of the swivel width can be set independently on the right and left. These values can even be adjusted in the storage process via the operator terminal CCI 800.
In addition, corner filling, an automatic level change as well as a continuous adjustment of the crop-discharge height and the individual setting of a maximum storage height are available.
With the StoreMatic-PRO, the user has three presets for the storage process ex works: Maximum performance, maximum crop protection or a middle way between high performance and high crop protection at the same time. With these presets, setting the required values of the store loader is much more intuitive.

“Flow Control” line control is available for all machines in the storage technology. Using this feature, the operator switches the entire storage line on and off in a defined, controlled sequence. The most important machine functions of the store loader can be controlled via the optional radio remote control.
Compact machine design
The new generation of store loaders immediately catches the eye with its open and slim machine design with the counterweights arranged on the sides of the chassis. This reduces the build-up of soil and dirt on the chassis and significantly increases accessibility for maintenance work. The drawbar can easily be swung out of the way, so you don’t need to remove it. The standard, hydraulic changeover between transport and swivel position is conveniently carried out via the control box.
The GRIMME Group
The family company GRIMME was founded in 1861 as a forge in Damme (Germany) and employs more than 2700 people worldwide.
GRIMME Landmaschinenfabrik has been manufacturing high-quality agricultural machinery for more than 80 years and is active in potato, beet and vegetable technology in over 120 countries around the world. The GRIMME Group also includes the companies ASA-LIFT in Denmark, SPUDNIK in the USA, INTERNORM and RICON in Germany, as well as 12 international sales and service subsidiaries.