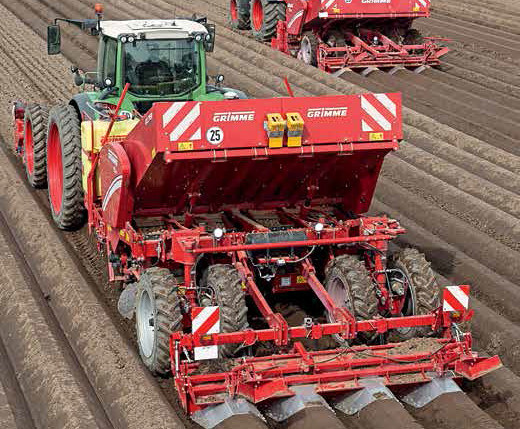
What provides a more even distance between seeds: belts or spoons? In the first part of our test, we will find out ..
Grimme GL 430, GB 430
Grimme offers a wide range of potato planters : 10 spoon models and 4 belt models. Spoon models range from 2- to 8-row; belt – from 2- to 4-row. Last spring, profi colleagues took a pair of 4-row machines – a 2012 GL 430 and a 2014 GB 430 – and ran them in parallel to find the differences. It is easy to remember who is who: the belt model has the letter B in its name (from the English belt, belt).
Each planter was attached to a 176 kW / 236 hp Fendt 724 tractor . with. A 3-meter rotary tiller Grimme GR 300 Rota Tilla, designed for pre-planting soil preparation for potatoes on non-stony soils, was also aggregated to it. The GL 430 spoon can be coupled with a drawbar, so a rotary cutter from Grimme, Amazone or Lemken can be installed between it and the tractor.
The belt machine does not have this option, in which case the Rota Tilla has been moved to the front attachment of the Fendt tractor. The specification of both planting machines was as follows:
– row spacing 750 mm;
– bunker volume 3.0 … 3.5 t;
– fertilizer application system;
– XL boards.
Let’s start, as usual, by connecting to the tractor. These trailed machines are coupled to it using the K80 ball hitch, which simplifies the process, reducing unnecessary maneuvers to zero.
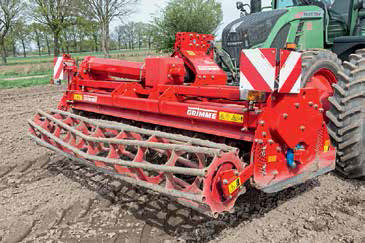
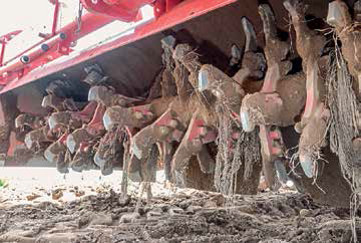
did its job well with 112 teeth
The belt model GB does not have a pipe holder, but on the other hand it has a hydraulic strut. GL at the time of the test had already “plowed” 1000 hectares, and during our work its drawbar cracked; now Grimme offers a repair kit to solve this problem, and new machines already have a reinforced drawbar.
We were very pleased with the performance of the Grimme GR 300 Rota Tilla rotary cutter. It requires less than 60 kW / 80 hp. with. and is capable of absorbing up to 186 kW / 250 hp. with., and its 112 teeth do not leave any lumps in the soil, it does not matter whether the milling cutter is used in the front hitch of the tractor or in tandem with the GL 430 at the rear. Front mounting is certainly not the best solution: in addition to adding almost 1.6 tonnes of weight to the front axle of the tractor, the Fendt front PTO had to be lengthened to the limit; in addition, the life of the automatic control system has become more complicated.
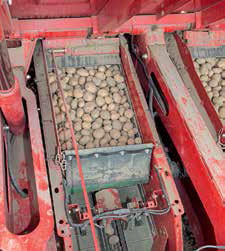
The length of the machine-tractor unit with Rota Tilla at the front is 14.7 mso it all takes up a lot of space on the road and in the field: 16-17 meter headlands are not enough for it. The GL 430 hopper has a nominal capacity of 3 tonnes, and the fill level check here showed full compliance with the specification, in contrast to the 3.5 tonne tipping belt model hopper, which contained 0.7 tonnes less.
Each machine travels on four wheels mounted in pairs at the rear of the planter. The GL we tested had 9.5×24 tires, barely enough for the stated load, although the wider 11.5 / 80-15.3 tires are now standard; the larger Grimme GB planter came to us with just these tires. Although modern GL planters have a swivel chassis with a steering option, the wheels of our older test car did not turn. The GB may also have a steering wheel steering axle, and our machine was also equipped with a Trimble GPS module for steering. After a lengthy adjustment of the automatic control, it provided straighter rows.
The furrow openers on both models are of the trailing type (that is, installed behind their legs) are mounted on a parallelogram mechanism. The furrowers on the GL 430 have hydraulic depth control; this gives excellent planting uniformity.
However, having worked on 1120 hectares of arable land, the 2012 model furrowers had obvious wear on the suspension – they were displaced approximately 50 mm back. As a result, tubers falling into the furrow could bounce off the metal structure. Therefore, before the test, Grimme replaced the furrowers together with the suspension. And the newer GB 430 uses a pair of gauge wheels to control the furrowers – they look more durable.
The heart of a planter is its planter.In the GL 430, it is a vertical 190 mm wide rubber belt for each row, on which spoons are staggered, gently gripping the tubers from the hopper. Grimme offers spoons in various colors to match tubers of various shapes and sizes; the greens we used are for medium tubers. All four belts are driven by one hydraulic motor.
A mechanical shaker (electric is optional) allows you to leave only one tuber in each spoon, gently throwing off all illegal aliens with a plastic wedge at the top of the belt. To ensure that the feed belts are always full, the optional bottom conveyor keeps the tuber “flow” constant, although on the GL 430 test the plastic sprockets and conveyor drive bearings have worn out after nearly 200 hectares.
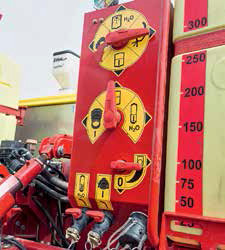
The GB 430 transports the tubers into the soil by means of several inclined belts.From the bunker, tubers enter the soil after passing three “floors”. First, they leave the hydraulically tiltable hopper through the infeed hatch and fall onto the conveyor. He feeds them into the second section, where angular sensors control the supply of tubers to six round belts; these belts gradually line up the tubers. A large foam roller at the front end of the belts slows down the tubers so that they fall evenly into the furrow.
The excess tubers are guided by a spiral roller from two return conveyors, one on each side of the main conveyor, back to the round belts. The speed of the belts (and therefore the distance between the tubers) is automatically controlled using information from an ultrasonic sensor that scans the flow of tubers that are planted in the soil.
There were also big differences in fertilization systems between the old spoon model and its younger belt cousin. The newer GB 430 has a pair of 400-liter spray tanks, a 95-liter fresh water container, a 61-liter / min pump, and automatically adjustable flow from three nozzles for each furrower. Its older sister, GL, has a more efficient pump, no clean water tank and only two nozzles per furrow. Both machines can be equipped to apply liquid fertilizers and pellets at the same time. no clean water tank and only two nozzles per furrow.
Both machines bury the tubers in the furrows with 510 mm scalloped discs. The latter did their job well, but the service life of the bearings should be more than 500 hectares of work, as it happened with us. Lattice Ridge Rollers are basic equipment, although both machines came with optional XL stainless steel Ridge Plates. They form a smooth ridge in soils ranging from light sand to heavy clay, but require more power from the tractor and also increase fuel consumption from 2 to 5 l / ha, depending on conditions.
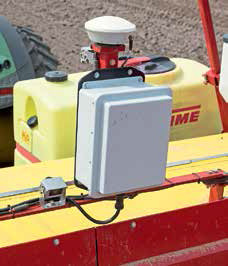
Time-consuming tuning will be required for quality work, especially if there is a 3-meter Rota Tilla in front
Synthetic linings protect stainless sheets from wear, but are not very durable – in the areas of contact with the ground, the protected metal began to wear out after 150 hectares of work. Replacing the liner is not a quick process (19 bolts on one pad) and quite expensive.
Which design provides the most accurate placement? To study this issue, we handed over both machines to machine operators, and then measured the distance between the tubers in the field. Each machine had to plant tubers in three sizes (35/45, 35/55 and 40/60 mm) at speeds of 6 and 9 km / h. In addition, two intervals were exhibited – 280 and 330 mm.
As you can see from the left side of the graphs on p. 21, at a speed of 6 km / h, the spoon machine had less deviation from the rating than the belt version, in particular, at 330 mm spacing. But at 9 km / h the situation changed and the GB belt machine deviated less from the target intervals (right side of the graphs). The size of the tuber also influenced the result. The belt model showed the most consistent results when planting small tubers; this is because the long oval tubers take up more space on the belt and fall off later. And the GL 430 spoon with large tubers could be better if the spoons were of the appropriate size.
What is the accuracy rating for these machines? It is believed that the spread of the interval from the specified 13–18% in each direction is acceptable. It turns out that none of the machines showed particularly impressive results.
Grimme agreed that better results could be obtained if more data were accumulated on working at different speeds and sizes of tubers. Overall, the belt machine was less stable in terms of spacing accuracy than the spoon machine, with variances ranging from 24% to 32%. Although, as already noted, the belt machine surpassed the spoon machine at a speed of 9 km / h.
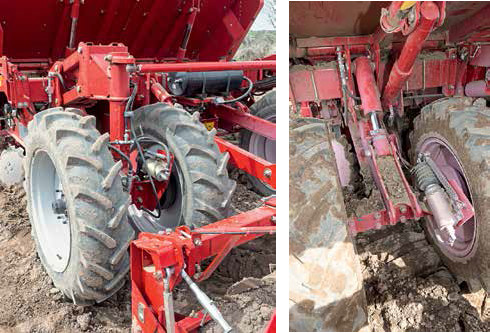
belt model was more likely to double , while the spoon GL 430 was less stable in skips and doubles at 9 km / h. In general, the latter showed more stable spacing between tubers when operating at a speed of 9 km / h.
Further details
– Grimme is supplying the GB 430 belt repair kit.
– We were not able to evaluate the fertilizer spraying or pellet delivery systems on these machines.
– The movement speed is measured with a sensor mounted on the GL quite accurately, since the gear wheel eliminates any slippage.
– The steering wheels of the GB belt help on the slopes, but it really makes the MTA difficult to control.
So: if you want speed, use belts. The GL 430 spoon model performs better with small to medium tubers and at a slow 6 km / h speed, although its performance with large tubers would probably be better if the correct spoons were installed. The belt model GB 430 surpassed the spoon model only at a high speed of 9 km / h.
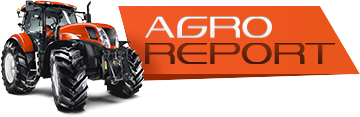