Peeling yield loss, is a term that relates to the good flesh and good useable potato that is wasted during the peeling process. This is measured as a percentage of the potato’s weight and varies on each potato.
Since the dawn of JIT, manufacturing companies have strived for greater productivity, higher quality, and reduced costs. Some think that they have set the bar relatively high, or perhaps they are content with the height they have established themselves, but standards are continuing to rise, and complacency will not help them reach their potential.
There is a quote by Seth Godin that says: “You can raise the bar or wait for others to raise it, but it’s getting raised regardless.”
The term implies that there must be a loss as part of the peeling process or that there must be a portion of good flesh wastage. But is this really the case? Could it be possible to have zero peeling yield loss?
The answer can only be found by challenging the experts to discover a better solution and elevating the bar yourself.
We have risen to the challenge – combining the leading peeling and sorting solution to form a total peeling module.
Decision making is controlled by the digital control center
Peeling alone can operate efficiently to peel less, but it is blind to raw material variations. Sorting alone can operate efficiently to control quality, but it is powerless to influence incoming quality. The total peeling module offered from TOMRA combines the best of both sorting and peeling, with the Digital Control Center of the unit making decisions in fractions of a second and reacting to variations in the raw material.

Using this combined approach, you achieve a compounding effect of performance improvement that is impossible with individual peelers and sorters alone. The Peeling Control Module (PCM) is the only one of its kind and forms part of the food process intelligence system, enabling companies to take a vital step forward in the industry’s push towards a digital transformation. It has been populated with data and programs to ensure that the variations in tuber varieties, sizes, and qualities can be scanned and uploaded to produce unique peeling module control programs.
Another equally important area where we raise the bar can be found in the uptime of the processing lines.
The digital transformation can already be seen around us, and everyday thousands of people manage the food supply chain, from the farm to our fork. Supermarket shelves are continuously filled with varied and exciting foods. Quick service restaurants receive deliveries of food daily to ensure that they can deliver high-quality food.
To satisfy the supply chain, food processing companies rely on equipment and technology more than ever before, and uptime becomes not only a performance metric but essential to keeping customers happy.
TOMRA Insight delivers near-live information about many connected devices by generating valuable data and processing it into actionable information. Our cloud-based service provides advanced warning of possible malfunctions by endlessly monitoring device and equipment sensor arrays and processing activity.

This information enables the line manager to plan for interventions and maintenance. With this knowledge, unplanned downtime has the potential to be a thing of the past.
I once heard a keynote speaker say that “TOMRA could revolutionize the use and re-use of resources worldwide.”
Then the speaker corrected themselves and said, “TOMRA has a responsibility to revolutionize the use and re-use of resources around the world.”
Raising the bar, step by step.

Topics: Potatoes, Vegetables news/processing/
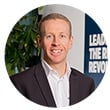
Written by Eamonn Cullen
Market Unit Manager Peeling – TOMRA Food Connect with me on LinkedIn