Imagine being a repairman sent to weld a patch on a leaky center pivot span in the middle of winter. Think of how helpful a photo or video of the water application and the leaks would be in helping you determine the location of the needed sprinkler repairs. Even the off-season task of changing out faulty sprinklers can be greatly reduced if you have video of the sprinkler application patterns from last summer to guide you to the location.
Many crop consultants have drone services available to video fields and equipment. Drones are becoming more common among irrigation and crop supply businesses. Once irrigators have seen drone video of an irrigation system applying water, drone services will likely be more in demand. The drone flies a path 40 to 50 feet above and parallel to the pivot from the center point to the end gun. A two- to three-minute video documents each sprinkler’s water pattern problems and visible leaks for later repair.
In August, staff from Michigan State University Extension and Purdue Extension performed a system uniformity can test on a 1,300-foot pivot near Sturgis, Mich. At the same time, a drone captured video images of the application and sprinkler. The concept is that taking a quick video of the pivot while applying water would allow a producer to identify needed repairs.
The example video showed a 1,300-foot pivot with one plugged sprinkler at the beginning that could be seen visually from the ground and corrected before the can test and the next drone flight. Three sprinklers were identified by the drone video that spun much faster than the others did, resulting in a smaller whipping application rather than the larger throwing pattern the sprinkler is designed to produce. The drone flight was videoed by John Scott, Purdue Extension digital agriculture coordinator, and Eric Anderson, MSU Extension field crop educator.
Scott found that by filming from above and to the side of the pivot, and aiming slightly ahead, the drone provided the best view of the water spray pattern and sprinkler repairs . Determining the best altitude and position to fly and the best angle from which to shoot video are matters of trial and error and depend on factors such as camera quality, crop, stage of growth, time of day and degree of cloud cover.

Identifying the needed sprinkler repairs areas of the application is the challenge. The repairs to our example pivot were simple and inexpensive: new caps for the damaged Nelsen 3000 sprinklers were purchased using the sprinkler chart to identify the correct parts. A trip to the local dealer and 10 minutes of climbing spans to replace the sprinkler tops corrected the problems. The sprinklers on our tested pivot contain a small resistance pump in the cap to regulate the spin of the deflector plate that creates the desired spray pattern.
When these wear out, the plate rotates much faster, creating a whipping effect and a much smaller throw. Three of the 131 sprinklers in the sprinkler package were replaced; replacing all the parts is recommended when the accumulated number of malfunctioning parts reaches 10 percent. Almost all sprinkler types will have a wear point that will need attention during their useable lifespan of seven to 10 years.
The irrigation system chosen for the study had its water supply flow tested to assure that the sprinkler repairs design was matched to water supply. Photos and video provide easy identification of differences between a given sprinkler and those adjacent to it. Pivots that have inadequate water supply flow for the sprinkler pattern will have a slowly decreasing application as you move from the center of the pivot length to the end gun, which may not be readily visible from photos or video.
There are common problems that greatly reduce water application uniformity from center pivots that our photos and drone video did not identify but our can test did. The drone footage did not capture the over-application area between the interface of an end gun and the sprinkler package identified by the catch can test. It did a good job of identifying sprinkler repairs out of sequence when we switched sprinklers, causing a double- and half-application mistake area.
A local pivot technician looking at the flight video said the video would be the perfect method to document what leaks and flanges need repaired on a unit. It would eliminate the necessity to turn the water on to identify leaks when a technician first gets to a site. A video from the ground would also work but would be much harder to get to in the middle of the season with standing crops in the field. Whether taken from the ground or a drone, a video sent to the repairman can be a huge benefit to identifying sprinkler problems.
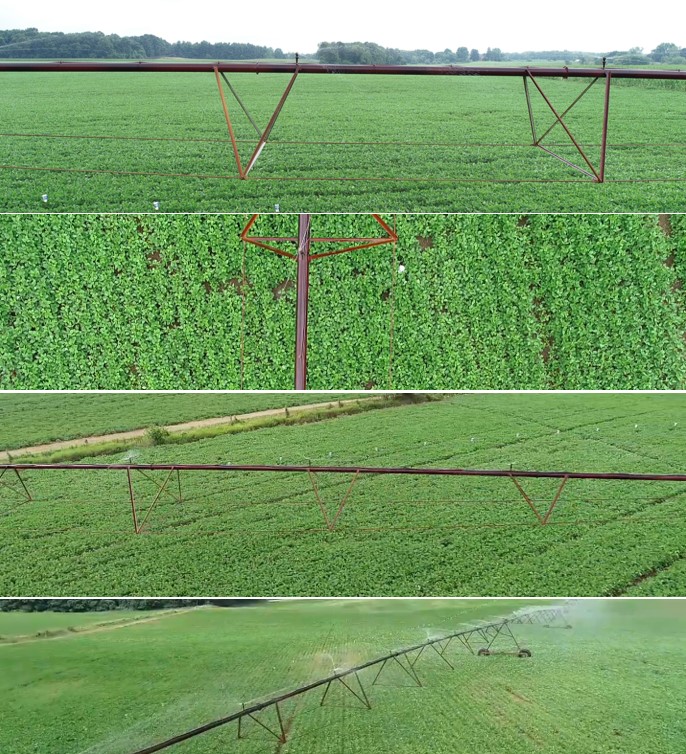
Lyndon Kelley is a water management and irrigation educator, and Eric Anderson is a field crops educator, both with Michigan State University Extension