If anyone can tell us the tips and tricks of proper maintenance of a plow, it’s him. Common thread: Rotating parts should be lubricated and worn grinding parts replaced in time. “If you keep muddling along, the team image will also change. Then you are already too late.”
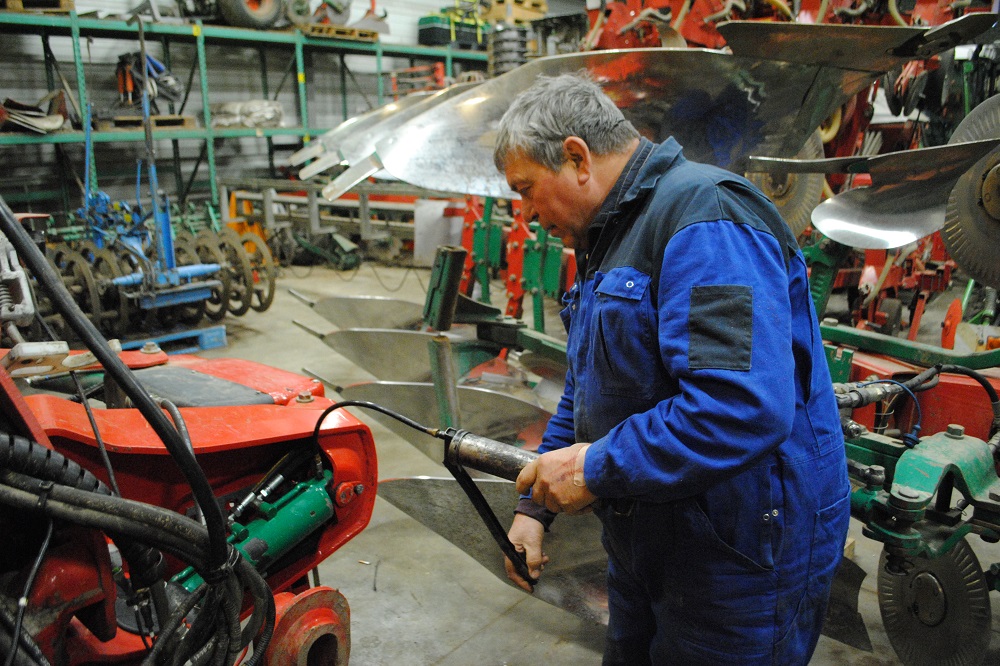
Maintenance neglected element
Buijs often sees things go wrong. The squad is part of the arsenal, but mainly because it is requested. Maintenance is then a neglected element. In arable farming, people are often very keen on it. “The plow is always cleaned after it comes off the land. Sometimes in the field it is a competition because the ground is hard or wet. It is then always checked whether bearings and bushings need to be replaced. If I want to buy a second-hand plow myself, I prefer to drive to Zeeland or Flevoland. The plows are well maintained there, much less so than, for example, dairy or pig farmers, who even have the plow outside. Sometimes the ground is even on it.”
Basis determines
According to Buijs, the foundation ultimately determines how it should be processed. “With plowing it is important to keep in mind that you do not cause structural damage. In the first place you need the root balls for the organic matter content. Secondly, this also ensures good water permeability. Thirdly, you want to get air into the ground. So don’t drive too fast, because that will make you throw and lose it on all three points.
With good plowing we get five percent more yield from the land. Much also depends on the team and its condition. In my view, the team will never disappear, because this operation leaves the best structure compared to all other alternatives.”
How do I maintain my team?
The ‘seven commandments of plow maintenance’ are explained in more detail in two parts. This section discusses the first four commandments.
1. Lubricate
“First you have to clean the team well. The rotating parts must be lubricated every day after plowing. Moisture can creep in, especially with wet soil. Consistent lubrication means preserving the discs and bearings. With proper maintenance, you should be able to work with discs for a thousand hours before they break. In the meantime, don’t forget to lubricate the vario. It doesn’t take twenty strokes of grease, one or two drops and then it’s lubricated again.”
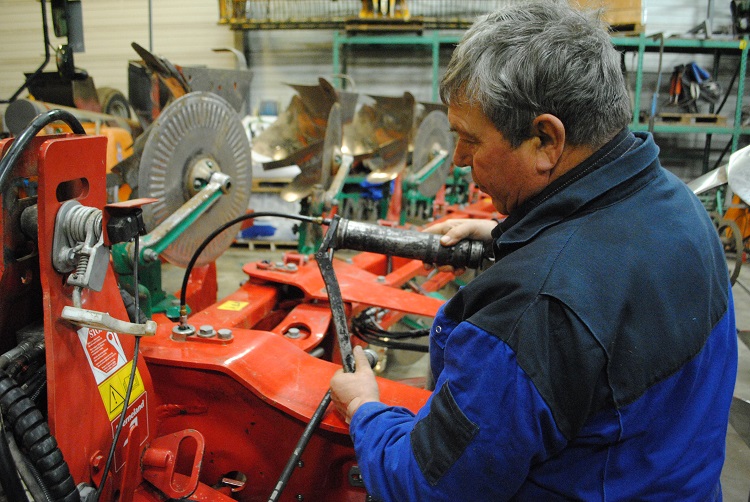
2. Check consumables
“The wearing parts have to be in good order. Holes or breaks should actually be seen two days before you really lose it or that it is broken. Also look at the team points. You often see it wearing down on the thin spots. It just wears faster there. Compare the wearing-in with respect to the header of the mouldboards. In the photo you can see that the tip of the front shear blade is almost gone.
So you have to replace it. Worn parts reduce cutting grip. Then you might say ‘I have GPS, so it doesn’t matter’. However, it is heavier. The squad twists. The plow image changes when there is wear. We replace something every year. The life of the mouldings and plow points depends on the soil type. On sand you can plow up to 350 hectares with the shears and 150 with the plow points.
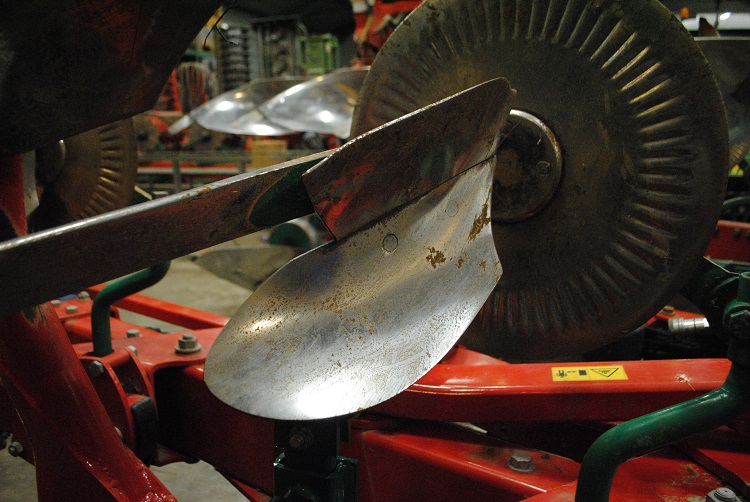
3. Tighten bolts
“Make sure you tighten the bolts a few times a year. They can vibrate and pull, especially on hard ground. Check it every time. According to the manual, especially if they are really new parts. Immediately after putting on for the first time and after plowing three or four times. That is often forgotten. I often come across the loose bolts in practice. The result is that the bodies come loose or you lose them while plowing. A loose part has an immediate effect on the team image.”
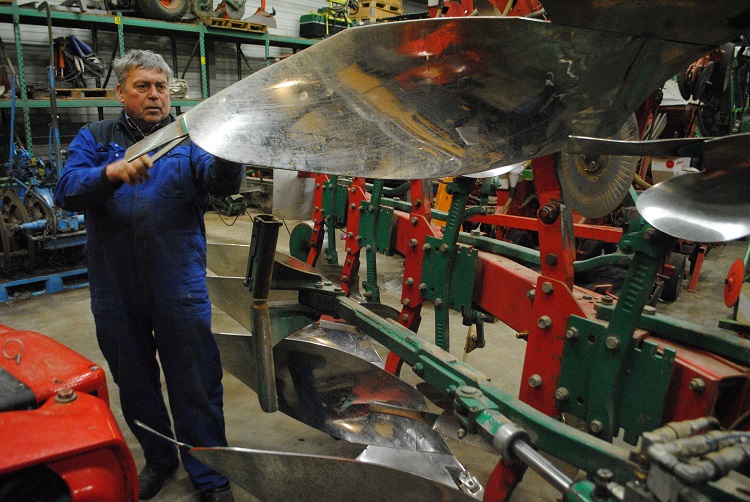
4. Measure geometry after
“For measuring the geometry, a folding rule and felt-tip pen is sufficient. The simplest is from the tip of the mold to the center of the other. Is it still right? If this is not the case, you can easily adjust the body and put it in the right place by pulling the rear bars in and out. If you have lost a bolt or a whole body, also check whether the geometry is correct.”
5. Check the electronics
“New plows have quite a lot of electronics, such as headland management and Isobus. Check that there are no breaks or tears in the cables and replace if necessary. A plow rotates and cables and hoses are destroyed. If a cable breaks, you’re done and you have to solve it in the field too, because you can’t go any further. In principle, calibration is not necessary. The mechanization man measures everything and you will never touch that again. You only have to adjust the depth and width from the cab.”
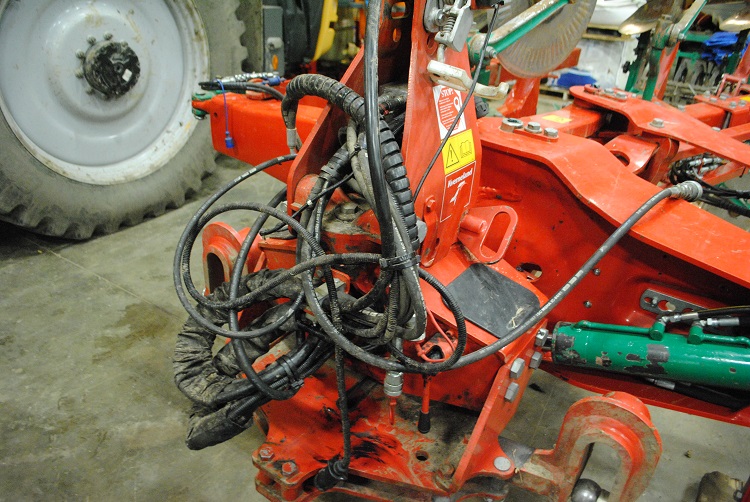
6. Look at the gauge wheel
“The gauge wheel must be free of play and must be able to adjust the depth as usual. The thread must be current. Remove it regularly and brush it clean, add new oil and you’re done.”
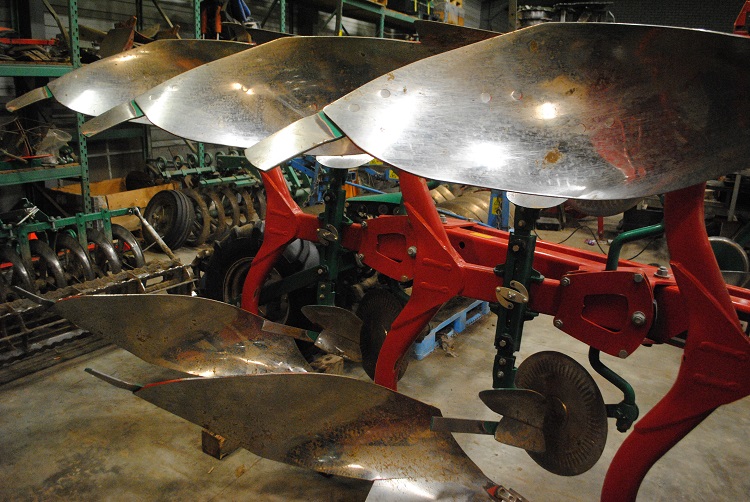
7. Don’t forget the three-point buck
“Maintaining the three-point stand that the team hangs on is also important. It does happen that the shaft shifts, making you plow narrow on one side and wide on the other. Look at it every time you come from the country. You saw it quickly. It is a rigid element, so no lubrication is necessary. The clamp in the photo is still OK, but make sure to replace any broken clamps as soon as possible.”
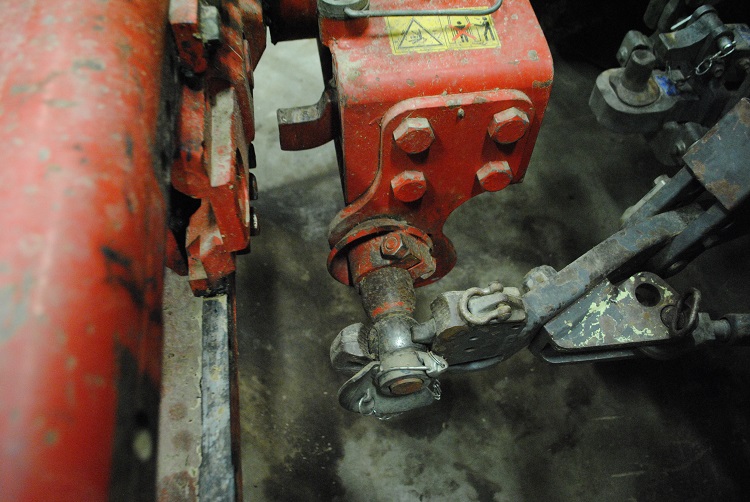